S
surfista
Forer@ Senior
Sin verificar
A partir de nuestro software de materiales, nuestras fuentes de información de Cartagena y los libros y web de materiales a las que estamos adscritos os explico un poco los pasos que hemos seguido para encontrar una aleación que se pueda usar.
En principio para crear un criterio de coherencia queremos hacer un diver con un metal que resista una presión hidrostática a 300 metros. Esto ocurre en las aleaciones de los submarinos, que suele ser en acero o en titanio. Como el reloj está diseñado en España queremos fabricarlo en las mismas aleaciones que el S60 y el S 80 que está construyendo Navegantia. El ingeniero naval me confirma que antes los submarinos españoles se fabricaban con un acero llamado A52, que ahora se usa en los encofrados para la cosntrucción. El acero que se usa actualmente en todos los submarinos del mundo es el HY80, el mismo de Sinn. El titanio ya no se usa porque según él es tan caro como el oro
. Nos informamos que los parámetros de dureza no interesan tanto como el módulo de elasticidad y la resistencia a la flexión. Por lo visto la presión hidrostática a 300 metros, que es de 3 MPA o 300 atm, debe de ser medida por el doble, es decir, 6MPA. Los parámetros que interesan son estos porque el submarino se comporta como un globo por la presión, es decir, mientras se sumerge se comprime, por lo tanto necesita un alto módulo elástico y cuando emerge se expande y necesita una alta resistencia a la tracción. Aparte de esto tiene que soportar un alto grado de corrosión del agua marina, que tenga un bajo contenido en níquel y que pueda ser mecanizado y pueda tener una buena terminación como un satinado o un arenado con micropartículas.
1º FASE CARACTERÍSTICAS DEL HY 80
Se puede comprobar la composición y propiedades de esta aleación. Es decir, hay un bajo contenido de níquel, una alta resistencia a la tracción y un elevado módulo de elasticidad. Necesitamos movernos en estos parámetros.
En la 2º fase vamos a ver qué metales necesitamos y comparamos con la corrosión del agua marina y el módulo de elasticidad.
2ª FASE DE INTERACCIÓN ENTRE MÓDULO DE ELASTICIDAD Y AGUA MARINA EN METALES
Aquí vemos la cantidad tales que resisten bien el agua de mar dependiendo de su módulo de elasticidad.
3ª FASE DE INTERACCIÓN DE RESISTENCIA A LA TRACCIÓN Y AGUA DE MAR
Estos son los materiales que resisten el agua marina. Como el número es muy alto, ahora tenemos que introducir los datos de la composición y en concreto las propiedades que requieren la aleación que necesitamos.
4ª FASE DE APLICACIÓN DE LAS PROPIEDADES Y COMPOSICIÓN REQUERIDAS PARA EL DIVER INSTANTE OCEÁNICO.
Se introdujeron los datos de composición, que fueron una base de Fe, con bajo contenido en C, o,20% y Ni 5%. Estos datos pertenecen a los valores del HY 80 y el bajo contenido de niquel era imprescindible ya que como médico creo que tenemos que pensar en que los aceros que usamos tengan el mínimo posible, para evitar las alergias.
El módulo de elasticidad y la resistencia a la tracción del HY 80 sugería unos parámetros de 205 MPA y 560 MPA respectivamente.
El resultado fue que nos quedaron 8 aleaciones de las 1000 y pico que habíamos empezado.
5º FASE DE PROCEDIMIENTOSNDUSTRIALES
En esta fase introducimos los procesos industriales que nos interesan que son el mecanizado y el acabado por chorro de arena.
6ª FASE RESULTADO DE LA ALEACIÓN PARA DIVER
La aleación resultante es la AISI 410 S recocida que en España es la UNE 36016 y la UNE 36257, con similar composición que el HY 80, permitiendo el arenado y el mecanizado, además de ser una aleación martensítica y no ferrítica, ya que estas suelen ser magnéticas. El módulo de young es de 210MPA y la resistencia a la tracción es de 500MPA
Deciros que esto ya lo llevamos madurando desde hace tiempo, que es un estudio teórico al que hay que darle viabilidad y si es verdaramente práctico utilizar este material para diver. El próximo paso es ponerme en contacto con el fabricante español para ver si el UNE 36016 da estas características.
Por otra parte, hoy estoy a caballo entre la consulta y la oficina ya que están casi pegadas. Alex y yo hemos estado haciendo este trabajo, mientras yo veo a mis chavales de ortodoncia. Espero que el mes que viene no me venga alguno de ellos con los dientes colgados del alambre
Un saludo
surfista
Bueno a ver que os parece
En principio para crear un criterio de coherencia queremos hacer un diver con un metal que resista una presión hidrostática a 300 metros. Esto ocurre en las aleaciones de los submarinos, que suele ser en acero o en titanio. Como el reloj está diseñado en España queremos fabricarlo en las mismas aleaciones que el S60 y el S 80 que está construyendo Navegantia. El ingeniero naval me confirma que antes los submarinos españoles se fabricaban con un acero llamado A52, que ahora se usa en los encofrados para la cosntrucción. El acero que se usa actualmente en todos los submarinos del mundo es el HY80, el mismo de Sinn. El titanio ya no se usa porque según él es tan caro como el oro

1º FASE CARACTERÍSTICAS DEL HY 80
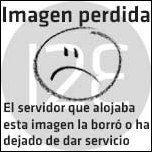
Se puede comprobar la composición y propiedades de esta aleación. Es decir, hay un bajo contenido de níquel, una alta resistencia a la tracción y un elevado módulo de elasticidad. Necesitamos movernos en estos parámetros.
En la 2º fase vamos a ver qué metales necesitamos y comparamos con la corrosión del agua marina y el módulo de elasticidad.
2ª FASE DE INTERACCIÓN ENTRE MÓDULO DE ELASTICIDAD Y AGUA MARINA EN METALES
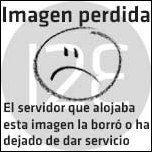
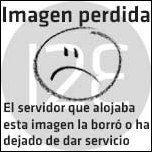
Aquí vemos la cantidad tales que resisten bien el agua de mar dependiendo de su módulo de elasticidad.
3ª FASE DE INTERACCIÓN DE RESISTENCIA A LA TRACCIÓN Y AGUA DE MAR
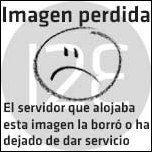
Estos son los materiales que resisten el agua marina. Como el número es muy alto, ahora tenemos que introducir los datos de la composición y en concreto las propiedades que requieren la aleación que necesitamos.
4ª FASE DE APLICACIÓN DE LAS PROPIEDADES Y COMPOSICIÓN REQUERIDAS PARA EL DIVER INSTANTE OCEÁNICO.
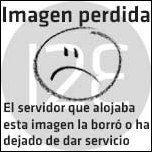
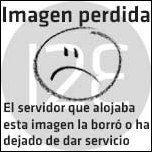
Se introdujeron los datos de composición, que fueron una base de Fe, con bajo contenido en C, o,20% y Ni 5%. Estos datos pertenecen a los valores del HY 80 y el bajo contenido de niquel era imprescindible ya que como médico creo que tenemos que pensar en que los aceros que usamos tengan el mínimo posible, para evitar las alergias.
El módulo de elasticidad y la resistencia a la tracción del HY 80 sugería unos parámetros de 205 MPA y 560 MPA respectivamente.
El resultado fue que nos quedaron 8 aleaciones de las 1000 y pico que habíamos empezado.
5º FASE DE PROCEDIMIENTOSNDUSTRIALES
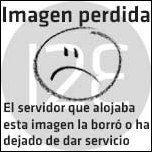
En esta fase introducimos los procesos industriales que nos interesan que son el mecanizado y el acabado por chorro de arena.
6ª FASE RESULTADO DE LA ALEACIÓN PARA DIVER
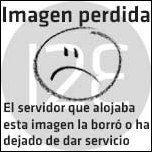
La aleación resultante es la AISI 410 S recocida que en España es la UNE 36016 y la UNE 36257, con similar composición que el HY 80, permitiendo el arenado y el mecanizado, además de ser una aleación martensítica y no ferrítica, ya que estas suelen ser magnéticas. El módulo de young es de 210MPA y la resistencia a la tracción es de 500MPA
Deciros que esto ya lo llevamos madurando desde hace tiempo, que es un estudio teórico al que hay que darle viabilidad y si es verdaramente práctico utilizar este material para diver. El próximo paso es ponerme en contacto con el fabricante español para ver si el UNE 36016 da estas características.
Por otra parte, hoy estoy a caballo entre la consulta y la oficina ya que están casi pegadas. Alex y yo hemos estado haciendo este trabajo, mientras yo veo a mis chavales de ortodoncia. Espero que el mes que viene no me venga alguno de ellos con los dientes colgados del alambre


Un saludo
surfista
Bueno a ver que os parece
Última edición: