
Suso
Antiguos Moderadores
Sin verificar
(NOTA: Este articulillo fue publicado por primera vez el 7 de Febrero de 2004, durante la Primera Edad de Relojes Especiales y ha tenido inestimables aportaciones de Hoyer y Goldoff)
PVD son las siglas de Phase Vapour Deposition (esto es, Deposición en Fase de Vapor para los que no dominen el inglés). Se trata de una forma de recubrimiento de metales en capas extremadamente finas pero de gran duración, y se puede llegar a las propiedades de los metales recubiertos.
De hecho, las primeras aplicaciones del PVD no fueron decorativas sino técnicas, siendo los recubrimiento de TiN (de color dorado, por cierto) los primeros en realizarse por este método. Tenían como finalidad aumentar la dureza superficial de las piezas de acero recubiertas, consiguiendo de esta manera una mayor resistencia al desgaste. Otros recubrimientos técnicos desarrollados posteriormente son los de TiCN, CrN, TiAlN-AlTiN .
Posteriormente se realizaron recubrimientos tribológicos, que son los que buscan no sólo mejorar la dureza de los materiales sino también las características de deslizamiento, rozamiento y autolubricación en contactos metal-metal que pueden dar lugar a gripajes, desgaste adhesivo o microsoldaduras. Estos recubrimientos suelen ser capas de sulfuros y carburos metálicos sobresaturadas de carbono.
Y luego llegaron los recubrimientos que a nosotros nos interesan, que son los recubrimientos decorativos. Es este caso, aparte de la función decorativa, se suele buscar una resistencia al rayado, al desgaste y a la corrosión. Es posible que la caja de nuestro querido Sinn 756 lleve algún tipo de recubrimiento PVD para lograr la dureza de su caja que lo hace tan resistente al rayado (1)
Existen varios métodos para lograr esos recubrimientos de PVD, pero la técnica consiste básicamente en vaporizar un metal puro o aleación del que vamos a recubrir la pieza por sublimación, obtener la reacción para obtener el compuesto deseado y depositarlo sobre la superficie de la pieza a recubrir (sustrato).
En un equipo se introducen las piezas a recubrir, con un baño de sales que contienen los iones que van a participar en la capa recubierta.
Al principio del proceso se practica un vacío inicial, y una vez se consigue éste, se introduce un flujo de gas inerte (Argón, generalmente).
Cuando se establecen las condiciones de atmósfera adecuadas, comienza un calentamiento controlado, hasta llegar a una temperatura en la que las sales se muestran en estado de vapor.
Estos iones, mediante un campo magnético dirigido, se cargan de forma positiva, y se proyectan sobre las superficies a recubrir.
El ión colisiona contra las partículas metálicas, desplazando a estas, ocupando su lugar. Esta colisión se repite millones de veces, a lo largo de toda la superficie del componente.
El grosor de recubrimiento se controla mediante el tiempo de reacción.
Con este proceso se consigue que las moléculas de material de recubrimiento entren a formar parte de la estructura molecular del metal (recordad las propiedades del enlace metálico que estudiásteis en química de bachiller o BUP). Es diferente de un chapado, ya que en los chapados existe una capa límite que separa el acero del oro. En el PVD esto no existe, ya que las moléculas de oro estan "incrustadas" en el acero.
En este esquema el átomo que da el color (oro, negro, rojo, azul, etc...) es el blanco y el sustrato (el acero) está formado por los átomos rojos.
Entiendo que todo proceso de recubrimiento requiere luego de un proceso de acabado, bien sea pulido, granallado (lo que en inglés llaman sandblasted), etc...
Los recubrimientos PVD son recubrimirntos metálicos y se les puede someter a aquellos procesos que se consideren necesarios para su acabado final. Lo único que hay que saber es que si te pasas, pues te cargas el recubrimiento y llegas otra vez al sustrato (recordad que la principal característica de este tipo de recubrimiento es que es muuuuy fino).
En cuanto a los colores, os he comentado los que yo he visto en relojes, pero en otras piezas los he visto azules, rosas, etc... todo depende de la composición de las sales que se van a usar para la obtención del recubrimiento y de la proporción de elementos en ellas.
Por poner un ejemplo, el recubrimiento con sales de TiAlN (nitruro de titanio y aluminio) -cuya principal característica es una gran resistencia a desgaste- proporciona un color que va del negro al bronce en función de la relación Ti:Al en la composición de las sales.
Otro ejemplo es el recubrimirnto de TiCN (cianuro de titanio), cuya característica principal es una mayor dureza superficial y menor coeficiente de fricción, tiene una gama de colores que va desde azul grisáceo hasta el rosa, en gunción de la relación Ti:C. Si a estas sales, además, se le añaden óxidos metálicos, el recubrimiento sale multicolor, que queda fashion-fashion.
Y aquí un par de aplicaciones prácticas, aportadas por Hoyer:
(1) Nota del moderador: En el caso del 756 no se trata de PVD, sino de un proceso de endurecimiento de toda la caja -de acero libre de níquel-: enfriamiento súbito con nitrógeno líquido: "La aleación de acero libre de níquel utilizada no sólo es perfectamente antialergénica, sino que puede ser endurecida en frío de tal manera que la caja acabada presenta una dureza Vickers de 710. Ese nivel representa una dureza de tres a cuatro veces la del acero normal y es la primera vez que este acero se usa en relojería".(de mi página)
PVD son las siglas de Phase Vapour Deposition (esto es, Deposición en Fase de Vapor para los que no dominen el inglés). Se trata de una forma de recubrimiento de metales en capas extremadamente finas pero de gran duración, y se puede llegar a las propiedades de los metales recubiertos.
De hecho, las primeras aplicaciones del PVD no fueron decorativas sino técnicas, siendo los recubrimiento de TiN (de color dorado, por cierto) los primeros en realizarse por este método. Tenían como finalidad aumentar la dureza superficial de las piezas de acero recubiertas, consiguiendo de esta manera una mayor resistencia al desgaste. Otros recubrimientos técnicos desarrollados posteriormente son los de TiCN, CrN, TiAlN-AlTiN .
Posteriormente se realizaron recubrimientos tribológicos, que son los que buscan no sólo mejorar la dureza de los materiales sino también las características de deslizamiento, rozamiento y autolubricación en contactos metal-metal que pueden dar lugar a gripajes, desgaste adhesivo o microsoldaduras. Estos recubrimientos suelen ser capas de sulfuros y carburos metálicos sobresaturadas de carbono.
Y luego llegaron los recubrimientos que a nosotros nos interesan, que son los recubrimientos decorativos. Es este caso, aparte de la función decorativa, se suele buscar una resistencia al rayado, al desgaste y a la corrosión. Es posible que la caja de nuestro querido Sinn 756 lleve algún tipo de recubrimiento PVD para lograr la dureza de su caja que lo hace tan resistente al rayado (1)
Existen varios métodos para lograr esos recubrimientos de PVD, pero la técnica consiste básicamente en vaporizar un metal puro o aleación del que vamos a recubrir la pieza por sublimación, obtener la reacción para obtener el compuesto deseado y depositarlo sobre la superficie de la pieza a recubrir (sustrato).
En un equipo se introducen las piezas a recubrir, con un baño de sales que contienen los iones que van a participar en la capa recubierta.
Al principio del proceso se practica un vacío inicial, y una vez se consigue éste, se introduce un flujo de gas inerte (Argón, generalmente).
Cuando se establecen las condiciones de atmósfera adecuadas, comienza un calentamiento controlado, hasta llegar a una temperatura en la que las sales se muestran en estado de vapor.
Estos iones, mediante un campo magnético dirigido, se cargan de forma positiva, y se proyectan sobre las superficies a recubrir.
El ión colisiona contra las partículas metálicas, desplazando a estas, ocupando su lugar. Esta colisión se repite millones de veces, a lo largo de toda la superficie del componente.
El grosor de recubrimiento se controla mediante el tiempo de reacción.
Con este proceso se consigue que las moléculas de material de recubrimiento entren a formar parte de la estructura molecular del metal (recordad las propiedades del enlace metálico que estudiásteis en química de bachiller o BUP). Es diferente de un chapado, ya que en los chapados existe una capa límite que separa el acero del oro. En el PVD esto no existe, ya que las moléculas de oro estan "incrustadas" en el acero.
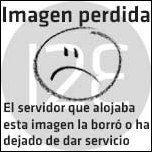
En este esquema el átomo que da el color (oro, negro, rojo, azul, etc...) es el blanco y el sustrato (el acero) está formado por los átomos rojos.
Entiendo que todo proceso de recubrimiento requiere luego de un proceso de acabado, bien sea pulido, granallado (lo que en inglés llaman sandblasted), etc...
Los recubrimientos PVD son recubrimirntos metálicos y se les puede someter a aquellos procesos que se consideren necesarios para su acabado final. Lo único que hay que saber es que si te pasas, pues te cargas el recubrimiento y llegas otra vez al sustrato (recordad que la principal característica de este tipo de recubrimiento es que es muuuuy fino).
En cuanto a los colores, os he comentado los que yo he visto en relojes, pero en otras piezas los he visto azules, rosas, etc... todo depende de la composición de las sales que se van a usar para la obtención del recubrimiento y de la proporción de elementos en ellas.
Por poner un ejemplo, el recubrimiento con sales de TiAlN (nitruro de titanio y aluminio) -cuya principal característica es una gran resistencia a desgaste- proporciona un color que va del negro al bronce en función de la relación Ti:Al en la composición de las sales.
Otro ejemplo es el recubrimirnto de TiCN (cianuro de titanio), cuya característica principal es una mayor dureza superficial y menor coeficiente de fricción, tiene una gama de colores que va desde azul grisáceo hasta el rosa, en gunción de la relación Ti:C. Si a estas sales, además, se le añaden óxidos metálicos, el recubrimiento sale multicolor, que queda fashion-fashion.
Y aquí un par de aplicaciones prácticas, aportadas por Hoyer:
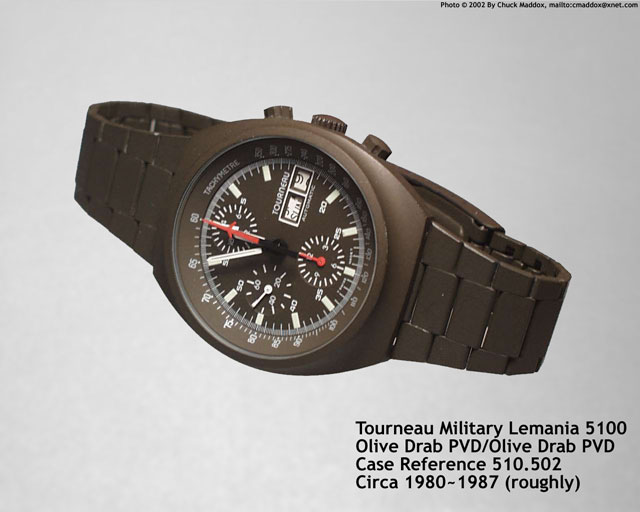
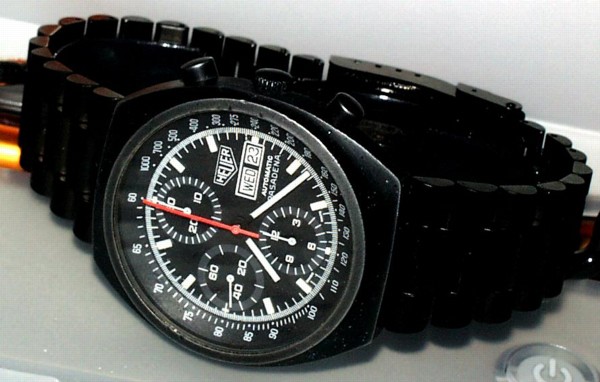
(1) Nota del moderador: En el caso del 756 no se trata de PVD, sino de un proceso de endurecimiento de toda la caja -de acero libre de níquel-: enfriamiento súbito con nitrógeno líquido: "La aleación de acero libre de níquel utilizada no sólo es perfectamente antialergénica, sino que puede ser endurecida en frío de tal manera que la caja acabada presenta una dureza Vickers de 710. Ese nivel representa una dureza de tres a cuatro veces la del acero normal y es la primera vez que este acero se usa en relojería".(de mi página)